Spritzguss Werkzeugbau
Die Qualität eines Kunststoff-Bauteils ist immer von der Qualität der Spritzgusswerkzeuge abhängig, mit denen Sie produziert werden. Deswegen liegt uns die Entwicklung und Herstellung von hochwertigen Spritzgusswerkzeugen ganz besonders am Herzen. Um unserem Anspruch gerecht zu werden, greifen wir auf modernste Technologien und unsere langjährigen Erfahrungen zurück – damit wir ihnen die bestmöglichen Resultate liefern können.
Unsere Leistungen
Ob die Entwicklung von Prototypen, Funkenerosion oder HSC Fräsen – wir erledigen für Sie alle Aufgaben, die im Bereich des Form- und Werkzeugbaus anfallen. Um bestmögliche Produkte aus einer Hand zu erzielen, greifen wir dabei nicht nur auf unsere Erfahrung, sondern auch auf modernste Techniken zurück, sodass Sie stets die besten Produkte erhalten. Nachfolgend liefern wir Ihnen eine Übersicht über unsere Leistungen und geben Ihnen einen kleinen Einblick in unsere Produktionsabläufe. Sollten Sie weitergehende Fragen haben, dann beraten wir Sie zu unseren einzelnen Leistungen ausführlicher – gerne auch persönlich.
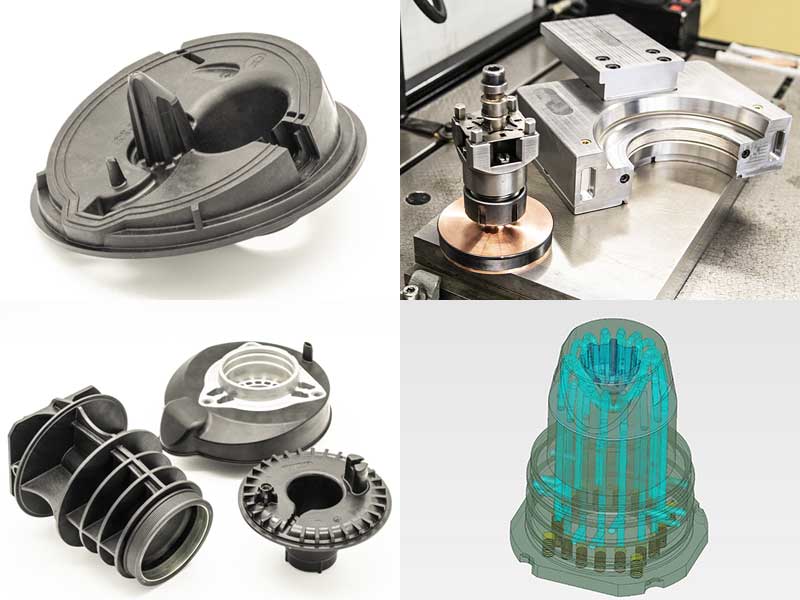
Herstellung von Spritzgusswerkzeugen
Eine unserer Hauptkompetenzen ist die Herstellung von Spritzgusswerkzeugen. Ein Spritzgusswerkzeug ist eine Dauerform, die man für die Produktion von Bauteilen mit Hilfe einer Spritzgießmaschine benutzen kann. Das Spritzgusswerkzeug wird in der Regel aus Metall gefertigt und umschließt einen Hohlraum, der die Form und Struktur des zu erzeugenden Bauteils aufweist. Dieser Hohlraum wird beim Spritzgießen dann mit einem plastifizierten Kunststoff befüllt. Anschließend kühlt dieser Kunststoff ab und wird hart. Ist das Material getrocknet, kann man das Spritzgusswerkzeug wieder öffnen und das Form- bzw. Bauteil entnehmen.
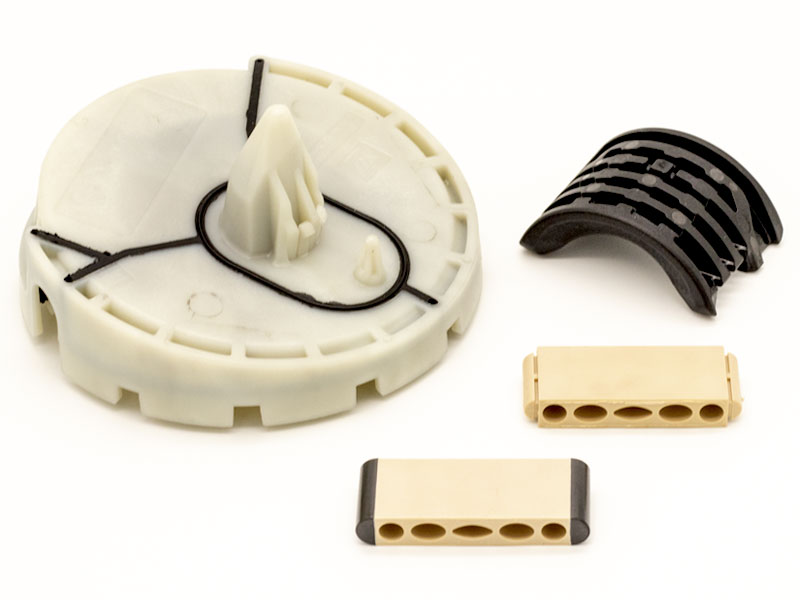
2 Komponenten Spritzguss
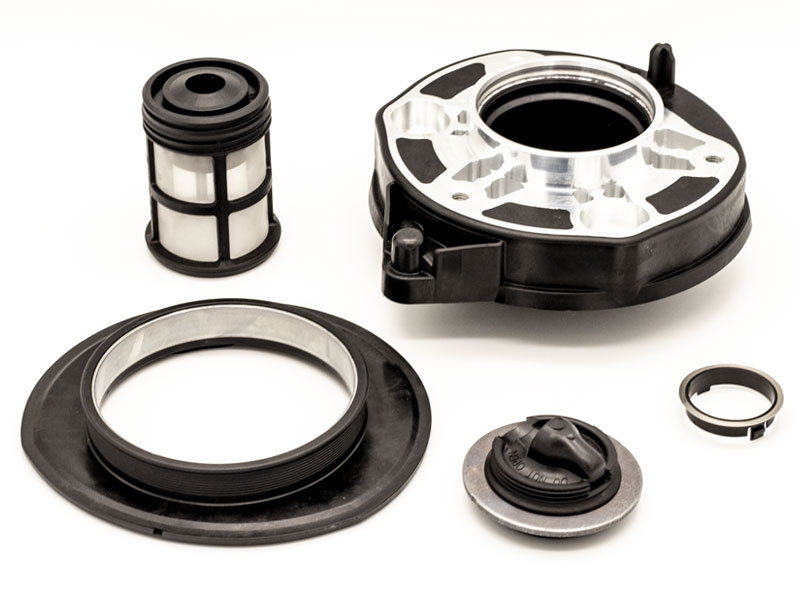
Einlegetechnik / Hybrid Spritzguss
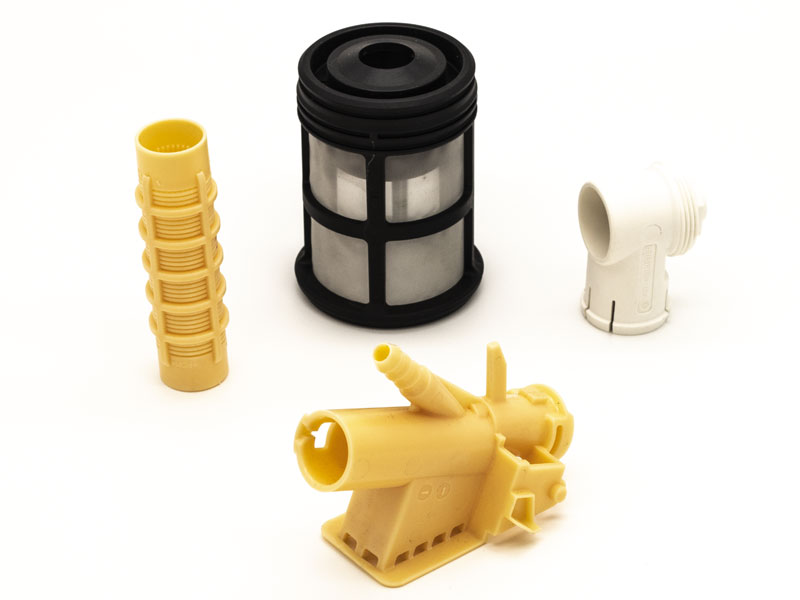
Filter- & Pumpentechnik
Spritzgusswerkzeuge eignen sich für die Produktion unterschiedlicher Bauteile und werden in der Regel für Formteile mit einem Gewicht von wenigen Dezigramm bis hin zu 150 Kilogramm verwendet. Auf Grund der effizienten und recht kostengünstigen Verfahrensweise ist das Spritzgießen eine beliebte Methode im Bereich des Werkzeugbaus und immer eine gute Wahl, wenn es um die Verarbeitung von Kunststoffen geht. Unsere Spritzgusswerkzeuge durchlaufen eine ständige Qualitätskontrolle, die bereits vor der eigentlich Produktion beginnt. Die Entwicklung und Herstellung der einzelnen Werkzeuge bedürfen nämlich einer genauen Planung. Im Rahmen der Arbeitsschritte überprüfen wir mit Hilfe von Berechnungen und Simulationen, ob das Werkzeug seiner Aufgabe ideal gerecht werden wird oder ob es eine weitere Optimierung benötigt.
Wenn wir ein Spritzgusswerkzeug entwickeln, fertigen wir als aller erstes eine Prinzipskizze an. Nachdem wir die Skizze angefertigt haben, bestimmen wir die Werkzeugtechnologie. Dieser Schritt erfolgt gerne in Absprache mit Ihnen, damit wir genauestens auf Ihre Bedürfnisse eingehen können. Als nächster Arbeitsschritt steht die Dimensionierung und die technische Auslegung des Werkzeugs auf unserer To-Do-Liste. Ist dies geschehen, stimmen wir das Werkzeug auf das Kunststoffmaterial ab, das später in ihm verarbeitet werden soll. Anschließend entwickeln wir das Angusssystem für das spätere Spritzgusswerkzeug und konstruieren die einzelnen Werkzeugelemente.
Finite-Element-Analyse (FEM)
Sind diese Arbeitsschritte abgeschlossen, nehmen wir eine Simulation des Füllvorgangs vor. Um ganz auf Nummer Sicher zu gehen, führen wir nun noch eine Finite-Element-Analyse (FEM) durch. Mit dieser lassen sich virtuelle Bauteile am Computer berechnen und Simulationen aufstellen, wie sich das Bauteil unter Krafteinfluss verformt oder verspannt. Die Geometrie der Bauteile kann dabei direkt aus einem CAD-Programm gelesen werden.
Für die FEM ist es dabei unerheblich, ob das Bauteil aus der Automobilindustrie oder dem medizinischen Bereich stammt. Sind die Berechnungen und Simulationen abgeschlossen, kann man anhand der Ergebnisse Rückschlüsse auf die Festigkeit und die Stabilität des Werkzeugs schließen. Der größte Vorteil der Finiten-Element-Analyse ist dabei, dass man virtuelle Prototypen entwerfen und diese testen kann, bevor man mit der mechanischen Konstruktion eines Werkzeugs beginnt. So lassen sich konstruktive Fehler bereits im Vorfeld erkennen und vermeiden, was mitunter viel Zeit und Geld einsparen kann. Erst wenn uns die Ergebnisse der Analyse überzeugen, beginnen wir dann mit der mechanischen Fertigung der Spritzgusswerkzeuge.
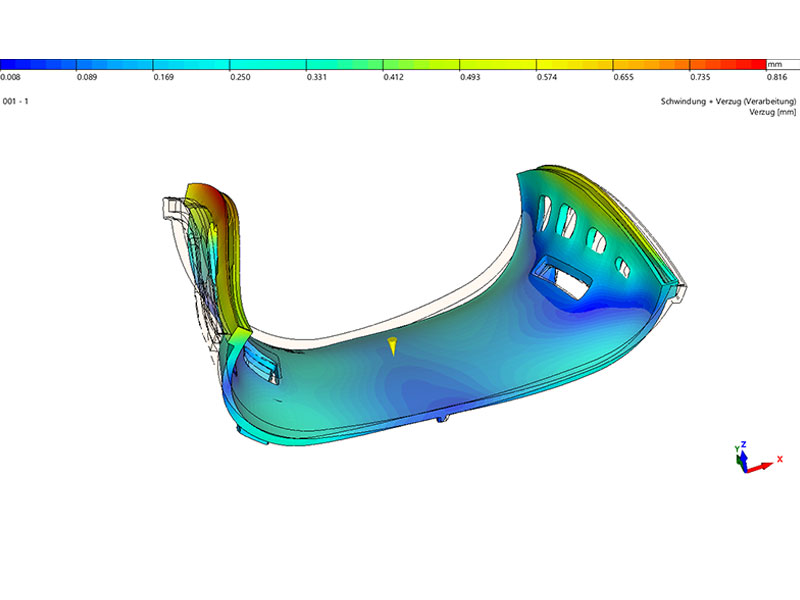
Wartung und Reparatur von Spritzgusswerkzeugen
Da auch die besten Spritzgusswerkzeuge mit der Zeit verschleißen können, ist die regelmäßige Wartung und Reparatur der Werkzeuge von großer Wichtigkeit. Eine kaputte Spritzgussform kostet nämlich nicht nur viel Geld, sondern kann auch dazu führen, dass ein Kunde verärgert wird, wenn es zu Verzögerungen in der Produktion kommt. Sollte eine Maschine auf Grund eines Defektes ausfallen, wird der Kunde im Zweifel nämlich warten müssen. Aus diesem Grund bieten wir auch einen Wartungs- und Reparaturservice für Spritzgusswerkzeuge an. Besonders dann, wenn man mit älteren Werkzeugen arbeitet, ist guter Rat oftmals selten, sollten die Maschinen einmal Schaden nehmen.
Dank unserer Erfahrung können wir aber auch in einem solchen Fall schnell reagieren und ihnen flexible Lösungen anbieten. Dank modernster Technik ist es uns dabei auch möglich, 3D-Dateien von älteren Einzelteilen anzufertigen. Mit Hilfe dieser Daten können wir die beschädigten Teile dann schnell reparieren und im Zweifelsfall sogar durch identische Teile ersetzen. Diesen Service bieten wir nicht nur Kunden an, die ihre Werkzeuge bei uns erworben haben, sondern auch Fremdkunden, die Probleme mit ihren Werkzeugen verzeichnen. In jedem Fall ermöglichen unsere gut ausgebildeten Mechaniker und Konstrukteure, unsere Erfahrung und unsere Moderne Ausstellung, eine flexible und effiziente Reparatur ihrer beschädigten Werkzeuge. Falls Sie weitere Fragen zu unserem Wartungs- und Reparaturservice haben, dann nehmen Sie gerne Kontakt mit uns auf.
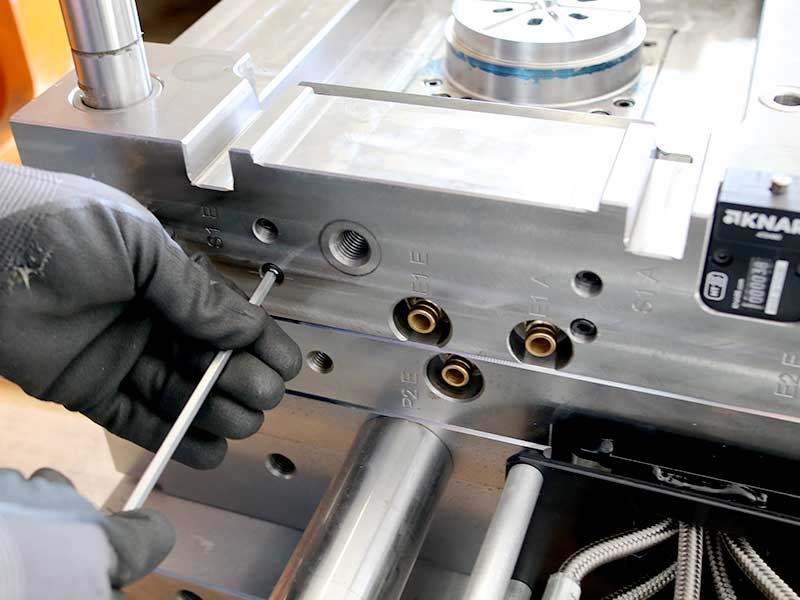
CAM/CAD
CAM ist die Abkürzung für “Computer Aided Manufacturing” und bedeutet, dass man auf Software und computergesteurte Maschinen zurückgreift, um Herstellunsgprozesse beim Werkzeugbau zu automatisieren. Dafür wird eine spezielle Software verwendet, um den NC-Code unabhängig von einer CNC-Maschine zu erstellen. Unter einer CNC-Maschine (Computerzied Numerical Control, dt.: computergestützte numerische Steuerung) versteht man ein Gerät, dass Maschinen steuert, in dem es Codes von einem Datenträger abliest und die gelesenen Steuerbefehle an die Maschinen weitergibt. Diese Steuerbefehle werden auf dem Datenträger als sogenannte NC-Codes hinterlegt.
Lange Zeit wurde die Programmierung von CNC-Maschinen in der Werkstatt vorgenommen, wobei man dementsprechend von einer Werkstattprogrammierung spricht (WOP). Dabei mussten die NC-Codes noch händisch in eine Eingabemaske getippt werden, was mitunter für Fehler sorgen kann. Durch das CAM-System ist dies aber nicht mehr nötig: Die NC-Codes lassen sich durch dieses nämlich noch während der Arbeitsvorbereitung erstellen. Hierbei kommt die CAD-Technologie (“Computer-Aided Design”) zum Einsatz, bei der das manuelle Anlegen von Modellen durch einen automatisierten Prozess abgelöst wird.
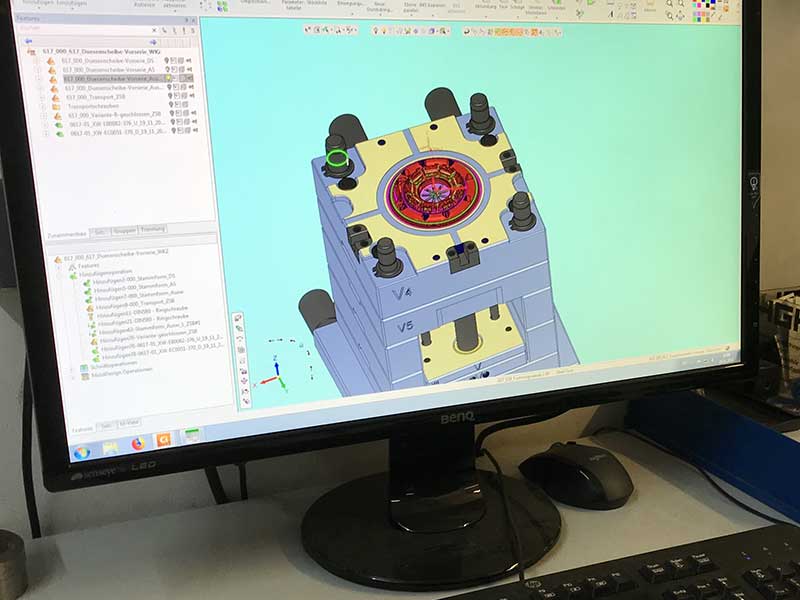
Mit Hilfe der CAD-Technologie lassen sich so digitale Konstruktionsmodelle erstellen, die dann in Form von CAD-Dateien über elektronische Wege an die CNC-Maschine gesendet werden. Diese liest die Informationen aus den im Modell gespeicherten NC-Codes und gibt die Steuerbefehle an die Maschinen weiter. Diese Form der Programmierung bringt einige Vorteile mit sich: Da so keine Geometriedaten mehr aus einer Zeichnung abgeschrieben werden müssen, können bei der Übertragung keine Fehler mehr gemacht werden. Außerdem muss der Anwender nicht mehr in der Werkstatt vor Ort sein, wie dies bei der WOP der Fall wäre, sondern kann im Büro sitzen, während die automatisierten Maschinen ihre Arbeit machen. CAM-Systeme sind dabei aber natürlich nicht umsonst und das Personal muss vor der Anwendung entsprechend geschult werden. Dann aber lässt sich mit diesem Verfahren eine Menge Zeit einsparen: Der Bediener der Maschine muss die Codes nicht mehr per Hand eingeben, wodurch Fehler vermieden werden und Zeit eingespart wird.
HSC Fräsen/ CNC Fräsen
“High Speed Cutting”, abgekürzt HSC, bedeutet im Deutschen soviel wie “Hochgeschwindigkeitszerspanung”. HSC kommt zum Einsatz, wenn man Metall mit einer CNC Fräsmaschine verarbeiten wird. Dabei ist nämlich eine hohe Schnittgeschwindigkeit und eine erhöhte Drehzahl des Werkzeugs nötig, wie man sie mit dem HSC-Verfahren erreichen kann. Neben diesen Vorteilen wartet HSC noch mit weiteren Vorzügen auf. Das Zeitspanvolumen etwa lässt sich um bis zu 30 Prozent steigern, während die Schnittkräfte um das 30-fache reduziert werden können. Dadurch lassen sich auch Objekte mit besonders dünnen Wänden fräsen. Die Vorschubs-Geschwindigkeiten fallen beim HSC fünf- bis zehnfach so schnell aus, als das beim konventionellen Fräsen der Fall ist. Außerdem verbessert sich die Oberflächenqualität der Werkstücke, wodurch ein nachträgliches Schleifen der Oberflächen obsolet wird. Gleichzeitig verzieht sich das Material im Zuge der Zerspanung nicht durch Wärmeeinfluss.
Das liegt daran, dass die Schnittgeschwindigkeit die Wärmeleit-Geschwindigkeit übersteigt, sodass die Wärme im Bruchstück bleibt. Mit dem HSC-Verfahren lassen sich zudem auch gehärtete Materialien mit einer Härte von bis zu 69 HRC verarbeiten. Dadurch erübrigt sich eine Härtung nach dem Fräsen und ein Härteverzug wird vermieden. Die hohe Oberflächengüte und die hohe Leistung des Zerspanens liefert auch Vorteile in Bezug auf das Vorschruppen und das Schlichten. Aufgrund der genannten Vorzüge kommt HSC in Gebieten zum Einsatz, in denen die Oberflächenqualität und die Zerspanleistung eine besonders große Rolle spielen. Das ist etwa beim Werkzeugbau oder dem Formenbau der Fall. Im Formenbau kommt das HSC Fräsen bei komplexen 3D-Konturen zum Einsatz, wie sie zum Beispiel beim Blasformen für Flaschen aus Kunststoff zu finden sind.
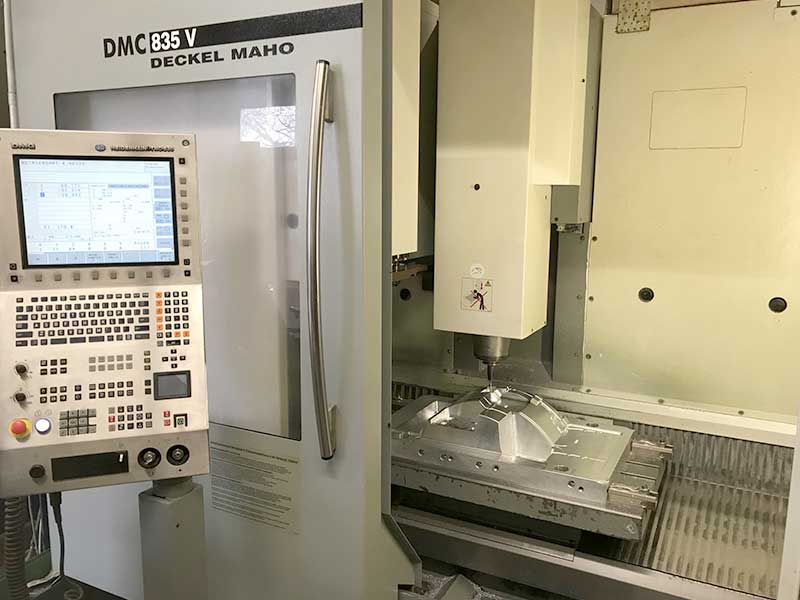
HSC Fräsen werden vorrangig in Kombination mit Fräsen benutzt, die aus feinem Vollhartmetall hergestellt werden. Diese nämlich sind in der Regel mit Hartstoff beschichtet und verfügen über eine spezielle Geometrie der Schneiden. Es kommen aber auch andere Schneidstoffe aus polykristallinem kubischem Bornitrid oder polykristallinem Diamant (PKD) zum Einsatz. In Kombination mit Wendeschneidplatten können im Rahmen des Formenbaus Konturen bearbeitet werden, wobei die Abstände der Fräsbahnen dabei gering ausfallen, um unterschiedliche konturen zu erstellen. HSC Fräsen weisen zudem eine hohe Rotationsgeschwindigkeit auf, da sie von Motorspindeln angetrieben werden. Dadurch ist ein sehr präzises Arbeiten bei einem beachtlichen Tempo möglich.
Senkerodieren und Drahterodieren
Senkerodieren und Drahterodieren sind Begriffe aus dem Kontext der Funkenerosion. Diese kommt bei der hochpräzisen Bearbeitung von Materialien zum Einsatz und ist ein abtragendes Fertigungsverfahren, das vor allem bei der Bearbeitung von elektrisch leitfähigen Werkstoffen alle Härten und Festigkeiten Verwendung findet. Die Funkenerosion ist besonders im Bereich des Formen- und Werkzeugbaus als Verfahren beliebt und wird häufig in Ergänzung zum Spanen eingesetzt. Bei der Funkenerosion wird das elektrisch leitende Werkstück – häufig aus Metall – in einer nicht leitenden Flüssigkeit bearbeitet. Diese Flüssigkeit heißt Dielektrikum und besteht in der Regel aus deionisiertem Wasser oder speziellen Ölen.
Bei der Funkenerosion können Ergebnisse mit Hilfe von zwei unterschiedlichen Verfahren erzielt werden: Mit Hilfe des Drahterodierens (funkenerosives Schneiden) und des Senkerodierens (funkenerosives Senken). Funkenerosives Schneiden wird bei der Produktion von Schnitt- und Stanzwerkzeugen, Extruderwerkzeugen, und Pofilwerkzeugen zur spanenden Bearbeitung angewandt. Ebenso kommt das Drahterodieren bei der Herstellung von Senkerodierelektroden und Prototypen zur Anwendung.
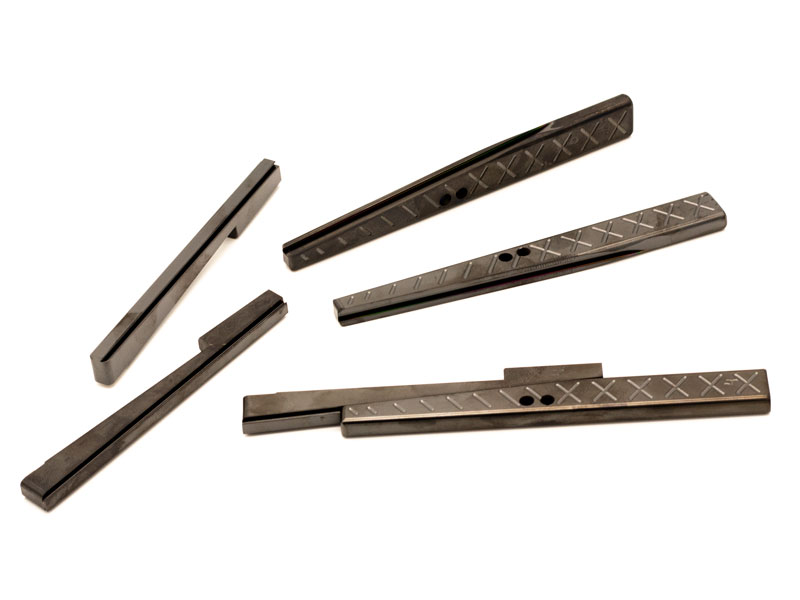
Beim Senkerodieren hingegen werden die Formen von Werkstücken mit Hilfe von Elektroden erzeugt, wobei die Elektrode dabei den Gegenpart zur geplanten Form des Werkstücks darstellt. Sowohl das Draht- als auch das Senkerodieren beruhen dabei auf demselben physikalischen Prinzip des Abtrags: Im Rahmen der Funkenerosion führen kurzzeitige, örtlich voneinander abgekoppelte Entladungen von Funken zu einem Abtrag des Materials. Dieser Abtragvorgang findet in einer dielektrischen Flüssigkeit statt, die elektrisch nicht leitend ist. Während die Elektrode und das Werkstück beim Senkerodieren in einem dielektrischen Bad liegen, wird beim Schneiderodieren ein Strahl aus Koaxial genutzt, der neben dem Dielektrikumsbad entlang der Drahtelektrode verläuft. Bei beiden Methoden werden jedoch dieselben drei Phasen durchlaufen:
1. Zündphase
Während der Zündphase befinden sich die positiv geladene Draht- oder Massivelektroden und das negative Werkstück in einem kurzen Abstand zueinander. Die Lücke zwischen den beiden Bestandteilen wird Arbeitsspalt genannt. Dank dieser Positionierung erzeugt das Anlegen einer elektrischen Spannung ein elektrisches Feld. Durch Stoßprozesse zwischen den beschleunigten Elektronen und Ionen wird kinetische Energie dann in Wärmeenergie konvertiert. Die nicht leitende Flüssigkeit, das Dielektrikum, verdampft in der Folge und es entstehen frische Ladungsträger. Daraufhin bildet sich ein Entladekanal in Gestalt einer Plasma-Gasblase, die man man anhand der auftretenden Funkenbildung erkennen kann.
2. Entladephase
In der Entladephase dehnt sich der entstandene Entladekanal weiter aus, wenn der Stromfluss steigt. Auf Grund der Zähigkeit des nicht leitenden Dielektrikums wird ein Gegendruck erzeugt, durch den der Entladekanal zwischen Elektrode und Werkstück ‘eingequetscht’ wird. An dieser Stelle kommt es zu einer erhöhten Stromdichte, was eine intensive Erhitzung zur Folge hat. Durch diese schmilzt und verdampft das bearbeitete Material.
3. Pausephase
In der Pausephase wird die elektrische Spannung abgeschaltet und die Energiezufuhr beendet. Dadurch platzt die Gasblase und die restliche Schmelze wird ausgeworfen. Die in Folge der Funkenerosion erhärteten Abtragspartikel werden im anschluss durch die umliegende, nicht leitende Flüssigkeit abtransportiert.
Elektrodenherstellung
Für das Draht- und Senkerodieren sind Elektroden notwendig, welche die entsprechenden Formen, die Passgenauigkeit und die benötigten Hinterschnitte erzeugen können. Gerade beim Senkerodieren spielt die Ableitung und Fertigung der passenden Elektroden eine wichtige Rolle. Bei der Herstellung von Elektroden leiten wir deren Form zunächst für das Senkerodieren ab und wählen anschließend das Material, aus dem die Elektroden dann gefertigt werden: Dabei lassen sich sowohl Elektroden aus Kupfer als auch aus Grafit erzeugen. Welches Material am besten geeignet ist, variiert je nach Verwendungszweck.
Gerne beraten wir sie dahingehend ausführlicher. Nach der Wahl des Materials wird mit Hilfe des CNC-Verfahrens ein Rohling aus Elektrolytkupfer hergestellt. Anschließend wird die Elektrode dem Feinschliff unterzogen und präzise nachbearbeitet. Im Laufe der Nachbearbeitung bringen wir die Elektrode in ihre endgültige Form. Bevor wir die Elektroden dann an unsere Kunden liefern, werden sie genauestens vermessen. Das Messprotokoll liefern wir Ihnen selbstverständlich gleich mit.
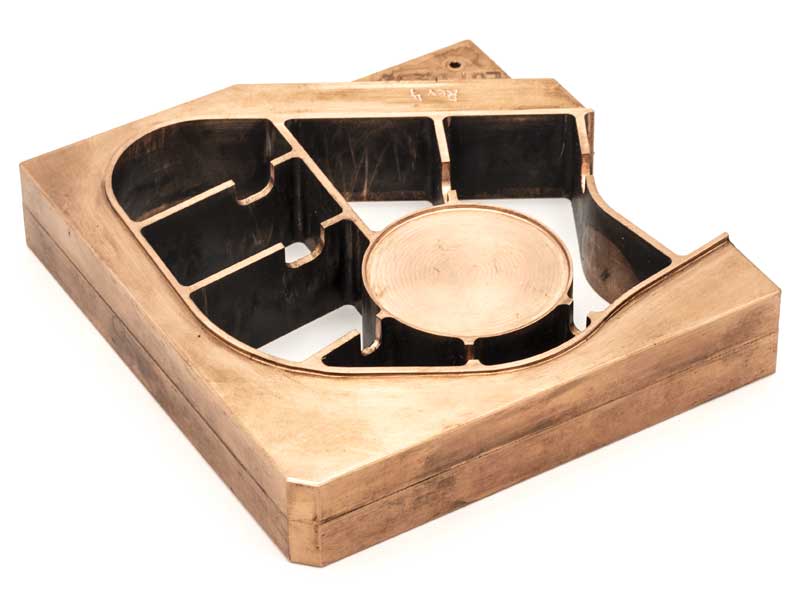
Musterung und Test
Bei der Produktion von Spritzgusswerkzeugen arbeiten wir mit höchster Präzision und führen genaueste Testungen durch, damit die fertigen Kunststoffteile die höchstmögliche Qualität aufweisen. Ein wichtiger Aspekt der Testphase ist die Anfertigung von Musterstücken, anhand derer wir die Eignung für Ihre Zwecke überprüfen – gerne auch in direkter und persönlicher Absprache mit Ihnen. Falls bei der Musterung erkenntlich wird, dass die fertigen Teile ihren Zwecken nicht gerecht werden, beraten wir Sie gerne dazu, wie wir die Bauteile weiter optimieren können.
Diese strengen Kontrollen ermöglichen es uns, qualitativ hochwertige Werkzeuge herzustellen, die sie im Anschluss für Ihre Produktion nutzen können. Damit die Ergebnisse am Ende bestmöglich ausfallen, ist aber auch die richtige Vorbereitung von großer Wichtigkeit: Je nach Verwendungszweck eignen sich verschiedene Kunststoffe unterschiedlich gut – bei der Entwicklung und Produktion von Kunststoffteilen gilt es schließlich, viele Faktoren zu beachten. Bevor wir mit der Entwicklung loslegen beraten wir Sie daher gerne, welche Kunststoffe sich für Ihre Vorhaben eignen und wie Sie ideale Resultate erzielen können.
Kontakt
Bitte nehmen Sie Kontakt zu uns auf, wir werden uns dann umgehend bei Ihnen melden.
Ihre Nachricht
*Pflichtfeld